Computational Fluid Dynamic Modeling of Geothermal Membrane Distillation
A 3-D COMSOL model was established to investigate the heat and mass transfer in a hollow fiber membrane (HFM) module for direct contact membrane distillation (DCMD).
Membrane distillation is a separation process that relies on vapor pressure gradients to drive the production of purified water across a hydrophobic membrane. In direct contact membrane distillation, both the hot water and cold permeate are in direct contact with the membrane. The temperature difference across the hydrophobic membrane induces the gradient of water vapor pressure resulting in desalination and water permeation through diffusion. COMSOL Multiphysics® was used to couple flow, heat transfer, and the transport of diluted species to simulate the conditions for bench-scale DCMD modules. The goal was to establish a CFD model that can be used to predict the performance of full-scale DCMD modules and to optimize the operating conditions for water production and energy consumption.
The microporous, hollow fiber membranes were made out of Poly(vinylidene fluoride) (PVDF) and each fiber has a nominal outer diameter and wall thickness of 800 and 100 µm, respectively. Membrane properties, such as pore size, porosity, thermal conductivity, etc., were measured and used as the inputs for the CFD simulation. Dusty-Gas Model was employed to describe the trans-membrane mass transfer of water vapor driven by Knudsen-molecular transition diffusion. Bench-scale experiments that employed the same module geometries and baseline operating conditions, were used for model validation.
Performance of the HFM in terms of water flux depends heavily on fiber packing configuration, packing density, and fluid flow rates. These parameters were modulated in the simulations to examine their effects on water flux. The main findings of the study were:
• Water flux is a strong function of the packing configuration. It doesn’t follow a continuous trend with increasing packing density, and is highly impacted by channeling.
• For a set packing density, water flux increases with increasing flow rate. The increase of flux due to flow rate gradually levels out for each packing density and packing configuration. There is a direct correlation between the flow rate and bulk temperature as well as between flow rate and the temperature polarization coefficient (TPC).
• High packing density (≥50%) is necessary to predict the water flux of an actual module using CFD simulations.
• Significance of the entrance and exit effects should be evaluated for modeling large scale modules for water flux predictions. CFD simulations of lab scale modules with and without these effect showed discrepancy of up to 25%.
• Single fiber CFD simulations cannot predict module performance accurately due to difference in velocity distribution and evaporative surface area.
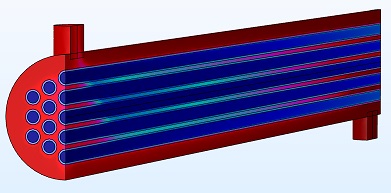
Téléchargement
- rivera_poster.pdf - 0.6MB
- rivera_paper.pdf - 0.81MB
- rivera_abstract.pdf - 0.02MB