Dosing of Food Pastes – Modelling the Flow of Highly Concentrated Suspensions Through Straight- and Converging Pipes
Food pastes generally consist of a viscous liquid phase in which a high concentration of solid fillers is embedded and their production often includes a dosing step that involves high speed extrusion. Due to the high volume fraction of solid fillers, this extrusion is not only subject to high operating pressures, but it also shows an increased risk of jamming, thereby blocking production lines and increasing machine downtime. Predictive modelling of paste flow could prevent these processing complications and help design processes and suitable product formulations. This paste flow modelling is relatively straightforward at low deformation and stress, since the paste can be regarded as a visco-plastic fluid and thus described as a continuum. However, during flow, local phase separation can introduce inhomogeneities that can lead to the formation of distinct flow regions. In straight channels, wall slip-, shear- and plug flow regions can co-exist, whereas the flow is further complicated at the entrance of confinements by static zones. Unfortunately, experimental determination of the individual contributions of the different regions has proven to be both difficult as well as time-consuming. By using COMSOL Multiphysics® the aim is to obtain a deeper understanding of the origin and effect of different flow regions and minimize experimental effort.
For this contribution we hypothesize that, as long as a lubrication layer of the liquid phase exists around solid particles, a CFD approach is capable of describing all flow regions. To test this hypothesis, experimental data is gathered from experiments performed on a custom-built ram extruder by adapting a Universal Testing System (Instron 3365, Instron, US). The extrusion pressures of an oil-based paste (sunflower wax, rapeseed oil and salt) are recorded at varying extrusion speeds through dies of varying confinement angle. The obtained data serves as input for our COMSOL Multiphysics® simulations, where the model is progressively made more complex to fit an increasing range of experimental data. The Optimization module is used to determine the model parameters and the resulting values are compared with measurements from supportive experiments and literature. Due to their elusive nature, special attention is paid to both the static zone as well as the slip layer. Since the existence of different flow regions makes a continuum approach difficult, an attempt is made to model the slip layer as a distinct phase. The thickness and rheological properties of the slip layer will be related to the bulk material (-flow), instead of using it as a boundary condition.
The simulations provide insight into the black box of paste extrusion, shedding light on the possible form and impact of the different flow regions. This is especially true for the development of static zones and slip layers, as their effect on pressure drop is difficult to measure and visualize experimentally.
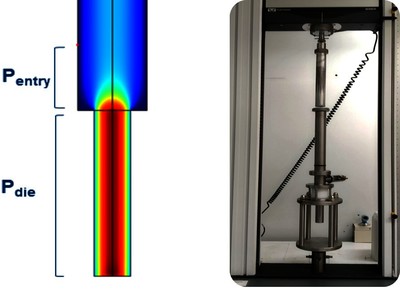