SpaceX Hyperloop Competition: Fluid Damper Optimization Through CFD & Multi-Body Simulations of The Prototype Dynamic Response to Stochastic Excitation
The EPFLoop team from Lausanne last year won the 3rd place in SpaceX’s Hyperloop Pod Competition in 2018. This year the team will participate at the 2019 Competition held at the SpaceX facilities California.
Reliability of the different subsystems constituting the pod is a key point. One of the main mechanical disturbance occurring along the run are the vibrations induced by the track inhomogeneities. At each beam junction, the whole structure is subjected to an abrupt change of rail center-line position and orientation. The alignment of the pod has to be optimized in order to ensure the Linear Induction Motor to operate at the nominal condition in term of efficiency and proximity to the rail. A good understanding of the vibration dynamics is also mandatory to ensure the integrity of each critical sub-components such as the batteries and electronics. Moreover, the reaction forces of each suspension system has to be evaluated to guarantee reliable connections with the carbon fiber composites.
The goal of this contribution is to optimize the pod behavior against vibration tuning the design parameters and characterizing the suspension system (namely spring stiffness k [N/m] and damping coefficient Cd [N.s/m]).
However, due to the lack of information concerning the misalignment distribution between the beams composing the rail, the transient response of the structure along the rail profile will be studied through stochastic approach.
The dynamic study is divided into two main models. In the first model the interaction between the pod and the rail will be modelled with the Multibody Dynamics and Lumped Mechanical System interfaces within COMSOL Multiphysics®. The eigenmodes of the pod will be inspected in order to understand qualitatively its dynamics without constraining the space parameters (k,Cd). This approach allows us to individuate the Pareto Front surface in the optimization problem for the (k,Cd) parameters and at the same time estimate the magnitude of variables such as displacement, rotation angle, pitch and roll during the run. The second model consists in simulating a fluid damper which composes the suspension system with a Computational Fluid Dynamics (CFD) simulation of the fluid damper. A further optimization process is needed in order to size the damper (through the diameter Dh on the piston through which the viscous fluid will pass) and the viscosity of the fluid (choosing the μ of the oil), considering the flow to be incompressible and Laminar. Hence, the Laminar Flow interface, coupled with the Heat Transfer in Solids and Fluids interface have been used. For each Cd the optimization will take into account two objectives; the maximization of the linear behavior of the viscous system and the maximization of its viscous drag component against its pressure one.
The models are interdependent and some iterations can be carried out for a fine tuning of the parameters. The outcome is a design that allows us to run the pod in the best conditions both for the positioning of the LIM and the integrity of the composite structure against reaction forces of the suspension.
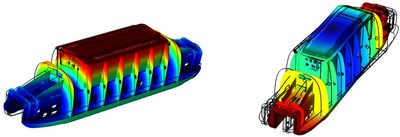