- Bridging the Terahertz Gap
- Modeling the Lithium-Ion Battery
- Protection contre la Corrosion
- Modélisation des batteries
- Modélisation et Simulation dans le développement des piles à combustible
- Modélisation thermique des petits satellites
- Analyse électro-vibroacoustique d'un transducteur à armature équilibrée
Concept Level Automotive Structural Analysis in COMSOL Multiphysics®
At the start of any automotive project, preliminary concept structures are generated which need to be analyzed in a fast and efficient manner. Concepts of different structural elements such as the chassis frame, cargo, Cross Car Beam etc. need to be optimized and front-loaded with vehicle performance targets as early as possible. As many utility vehicles are still have body-on-frame construction in India and considering the impact of frame design on the product development process, this paper will focus on frame concept development and analysis. Static analysis of ladder frames is attempted in COMSOL Multiphysics® using the structural mechanics module. Parametric 3D-geometries are built in the CAD environment in COMSOL Multiphysics® using built-in geometric shapes for each structure. Wherever possible, the geometry is linked to a vehicle dimension in order to understand its impact on the system. Material properties of the structure are inserted, and the model is meshed with beam elements. The section of each beam is inserted as input using the commonly used section types such as pipe, box hat etc. which are pre-defined in COMSOL Multiphysics®. The model is loaded and constrained as per the testing standard in the Stationary Study in COMSOL Multiphysics®. The resulting displacements and stresses are evaluated and the final performance parameters such as the bending stiffness and torsional stiffness are derived. For eigenfrequency analysis, the same meshed model is simulated to get the global frequencies and mode shapes. These values are validated with the physical testing and a correlation of more than 80% was achieved. These models are useful in doing parametric sweeps to understand the sensitivities of different parameters on the performance of the structure. The advantage of beam modelling over the detailed 3D CAE workflow is the speed at which analysis can be completed. Multiple concepts can be assessed for different parameters very quickly. The COMSOL Multiphysics® model is also converted to Application using App Builder. This gives the design engineer to have an interface having desired sets of inputs and output, which reduces the effort and gives out the results even faster. The application is uploaded in COMSOL Server™ which gives a platform for authorized users inside the organization to access the apps. An executable(.exe) file is also created to get access to the application without the requirement of a license. This study enables front-loading of global stiffness, modal frequency, durability and weight targets of the vehicle in early stage of product development. It also helps the design engineer to identify the good and bad design space and gives an efficient initial values and range of parameters to proceed. With this knowledge, efficient concept generation and evaluation takes place which speeds up the product development process.
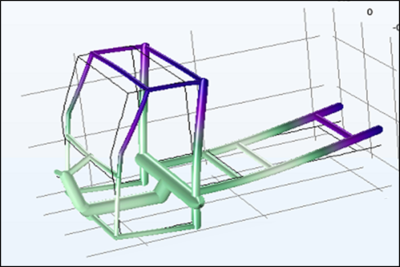