- Bridging the Terahertz Gap
- Modeling the Lithium-Ion Battery
- Protection contre la Corrosion
- Modélisation des batteries
- Modélisation et Simulation dans le développement des piles à combustible
- Modélisation thermique des petits satellites
- Analyse électro-vibroacoustique d'un transducteur à armature équilibrée
Performance Modelling of Gas Thrust Bearing
Gas lubricated bearing has been developed for high accuracy in precision machines and equipments. Gas lubricated bearings are mainly two types: aerostatic bearings, which require a feed of pressurized gas for their operation, and aerodynamic bearings, which generate their own internal pressure differentials. The latter generate this pressure by the action of simultaneously shearing and squeezing the environmental gas between the surfaces in relative motion and which is to be supported one upon the other, whereas the former require an external pump to produce the pressure. Though the loading capacity of the aerostatic bearing is confined by compressibility of air, the variation of its air-film thickness is significantly influenced by the applied load, the design parameters, and the operational parameters. Unlike conventional ball or roller bearings, there is zero friction between the bearing surfaces and thus become very popular choice for ultra precision application like precision linear stages. Fluid film lubrication problems that include gas bearings, traditionally been analysed using the Reynolds equation and this equation continues to provide remarkably accurate solutions in most cases. The growing interest in creating simulation to describe behaviour in condition where some of the assumptions used by Reynolds are invalid, such as where fluid inertia is significant, turbulent flow or cavitation occurs or fluid responds viscoelastically. Owing to availability of commercial CFD software codes based on the Navier-Strokes equations together with ever faster, low const computers have greatly reduced the effort to implement the same. In the works, various configurations of gas thrust bearings are solved using COMSOL multi-physics and presented here. Derived results such as load capacity, stiffness and mass flow rates are plotted against supplied pressure, bearing clearance etc and compared with experiments. The results show that CFD can model even model geometries of high aspect ratio ( ie 1000 or more) which is often the case in bearings.
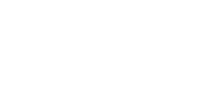
Téléchargement
- Murmu.pdf - 0.16MB