Development of a Mathematical Model for an Anode Baking Process with COMSOL Multiphysics®
The anode baking process has gained significant attention since the 1980s due to its importance in Aluminium industry. A good anode baking process strives to achieve multiple goals including reduction of NOx from emissions. NOx generation is mainly due to the high-temperature distribution around the burner and the air to fuel ratio. Therefore, understanding of the physical phenomena around the burner is of importance. The mathematical model in this respect can provide significant information.
The underlying problem of NOx optimization in anode baking furnace is characterized by the different physics such as the turbulent flow of air and fuel, combustion of fuel and volatile matter, heat generation due to combustion process, conjugate heat transfer through walls and radiation. The objective of this work is to systematically develop the mathematical model of the anode baking process by considering all the physical phenomena. As a first step, the CFD module of COMSOL Multiphysics® software is used for comparing two turbulence models namely Spalart-Allmaras and realizable k-ε. These models are analyzed based on their behaviour with respect to the boundary layer mesh and results are compared with another simulation environment. As a next step, chemical species are added by using ‘Transport of concentrated species’ interface of COMSOL Multiphysics® software. ‘Heat Transfer in Fluids’ interface with surface to surface radiation is applied to deal with the heat generated by combustion process and heat transfer through radiation. Conjugate heat transfer is modeled by adding the appropriate solid domain. The combustion reaction of fuel and air is defined using the eddy dissipation model. ‘Round jet burner’ tutorial from the application library is used as a reference. The complexity of the furnace geometry and underlying boundary conditions make this model highly non-linear. Techniques such as non-linearity ramping are implemented using auxiliary sweep to deal with this non-linearity.
The investigation suggests that the numerical convergence of the Spalart-Allmaras model in COMSOL Multiphysics® is highly sensitive to boundary layer mesh due to the absence of wall functions. The accurate comparison of turbulent flow with another simulation environment namely the IB Raptor code [1] is obtained only after refined mesh around boundaries and increasing accuracy of linear solvers. The results obtained by solving mathematical expressions for all physical phenomena align with the expected finding i.e. the reaction occurs immediately after mixing of air and fuel as the eddy dissipation model is used. The temperature profile is such that the maximum temperature is obtained at the interface of air-fuel reaction. The numerical convergence of the model combining all physics also depends highly on the mesh near the boundaries.
In this work boundary conditions that lower the non-linearity of the equations are applied. However, in order to compare results with actual furnace conditions, tools that can resolve highly non-linear equations would be needed. With such tools, it is expected to obtain a mathematical model of the furnace that can be used to optimize parameters to control NOx generation without compromising on anode quality.
[1] Talice, M., Lampitella, P., and Fiorini, M. Pm2 engineering.https://www.pm2engineering.com/
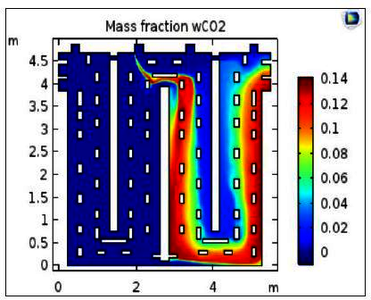
Téléchargement
- nakate_poster.pdf - 0.82MB
- nakate_paper.pdf - 0.61MB
- nakate_abstract.pdf - 0.02MB