Implementation of an Active Fluid Cooling Design in a 48 V High-Power Battery Module
Individual batteries have their own operational temperature ranges, which shall be respected to avoid both damaging of the cells and shortening of the cycle life. In terms of the Li-Ion cells, many of them do not function well at higher temperatures. Therefore, a better understanding of the thermal behavior of individual cells within a battery system, which can be achieved through simulation models, has its significance in designing safe and robust battery packages for automotive applications.
This study dedicates to analyze the thermal behavior of a 48 V automotive battery module and seeks smart designs for active fluid cooling. In order to suppress aging process while maximizing capacity retention of the cells, it’s one of the primary goals to maintain the temperature of all cells not only below the given maximal operational temperature, but also below app. 40 °C. The other objective of this study is to minimize the differences in cell temperature aiming at minimizing the differences of the cycle life of cells within the same battery module.
During this study, the Heat Transfer Module, the Pipe Flow Module and the AC/DC Module of COMSOL Multiphysics® are utilized to analyze the thermal behavior of a battery module. The study is carried out with following steps: [1] 3D time-dependent model of the battery system is constructed within the Conjugate Heat Transfer interface. The construction of cells and definition of the load profile are derived from the technical data of a suitable candidate for automotive applications. The temperature distribution in the ground model (no cooling system) is greatly uneven, which will lead to differences in cell cycle life within the same battery module in the long term and hence a shortened cycle life of the entire module. [2] By implementing various passive cooling designs, the differences in cell temperature within the battery module is restricted to. The temperature of the hottest cell maintains less than 40 °C at the stable state. [4] By employing active fluid cooling systems on top of the ground model or combine with passive cooling designs, the heat dispersal is accelerated through heat conduction and convection. [5] A smart solution - a combination of different cooling principles – is demonstrated in this study to maintain low operating temperatures for all cells and restrict the differences in cell temperature within the battery module.
Active fluid cooling systems shall be considered as an indispensable component in high power battery systems for automotive applications. Combined cooling systems with different cooling principles (active and passive systems) shall be involved for large and especially for high power battery modules, in order to achieve a homogeneous temperature distribution and ensure the function of all cells.
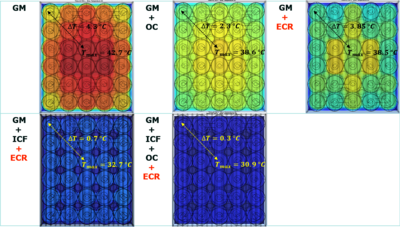
Téléchargement
- wu_presentation.pdf - 1.69MB
- wu_poster.pdf - 3.09MB
- wu_abstract.pdf - 0.57MB