Multiphysics Modeling of the Graphite Electrode Joint in Electric Arc Furnaces for Steel Recycling
Electric Arc Furnaces (EAF) use graphite electrodes to strike an arc to melt scrap steel, recycling it for further use. These graphite electrodes oxidize and are consumed over time. To maintain operation new electrodes are attached to others via a joint of complex geometry and fed through the system to provide semi-continuous operation. This joint is composed of two electrode ends, each with machined internal threaded sockets on both ends, as well as a pin with external threads; the pin and the electrode materials may have very different, anisotropic, and temperature-dependent thermal, mechanical, and electrical material properties, leading to a highly non-linear state. The joint provides a point of mechanical failure, leading to breaks which both incur acute costs to operators and increase electrode consumption costs. GrafTech has developed a finite element model to simulate the Joule-heating-driven stress distribution at the electrode joint, and used it to design improved joints and materials that reduce the probability of breaks and decrease electrode consumption rates. The model presented embodies a Multiphysics approach, with fully coupled electric currents, heat transfer with radiation, structural mechanics, and moving mesh to simulate oxidation. All the relevant physical contact mechanisms are accounted for by including mechanical, thermal, and electric contact. The simulation is transient, and incorporates real-life heating/cooling profiles, along with varying furnace operating conditions. The model is optimized for simulating small geometric tolerances, on the order of microns, to study not only geometric specifications, but also the effect of real-life tolerance ranges. Over one hundred cases have been simulated, varying material properties, geometric specifications and tolerances, along with other parameters. Multiple areas of focus were studied, both by DOE and One-Factor-At-A-Time sets of simulations. It was discovered that different modes of electrode mechanical failure correspond to different heating profiles and different times in those profiles. It was also observed that stress distributions and stress magnitudes may be significantly influenced by machining specifications and tolerances. Finally, it was predicted that material properties, their temperature-dependence, anisotropy, and the property differential between the electrode and the pin have a meaningful impact on the stresses and performance of the electrode system.
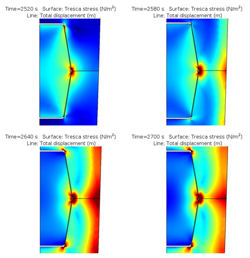
Téléchargement
- may_presentation.pdf - 2.42MB
- may_abstract.pdf - 0.01MB