- Bridging the Terahertz Gap
- Modeling the Lithium-Ion Battery
- Protection contre la Corrosion
- Modélisation des batteries
- Modélisation et Simulation dans le développement des piles à combustible
- Modélisation thermique des petits satellites
- Analyse électro-vibroacoustique d'un transducteur à armature équilibrée
Analysis of Flow in a Microfluidic Device: Pressure Drop, RTD and Mixing
Continuous flow reactors are recently being used for lab scale synthesis as well as pilot scale manufacturing of high value low volume chemicals. Here we present our work on a new configuration of flow reactor that includes several 1800 bends and yet a varying radius of curvature thereby yielding continuous change in the direction of streamlines. Experiments as well as simulations (in COMSOL Multiphysics® software) were carried out for 2D as well as 3D geometry to get an estimate of the pressure drop, residence time distribution and flow pattern in the reactor for a wide range of flow rates. Typical simulated flow pattern in part of the reactor and RTD curves at different flow rates are shown in Fig.1. A strong secondary flow was seen to get generated from the curvature of the channel which helped continuous mixing as the fluid travels from inlet to outlet. From the pressure drop data we also calculated the friction factor for the curved channel and compared the values with the friction factor values for a straight channel of the same length. Friction factor values of the curved channels were correlated with the extent of increase in the radius of curvature and the Re. Dispersion co-efficient and vessel dispersion number was calculated from the experiments as well as simulations. The values of the dispersion coefficient increases with the increase in Re and the experimental D/uL values clearly indicate that the flow inside the reactor channel is largely deviated from plug flow.
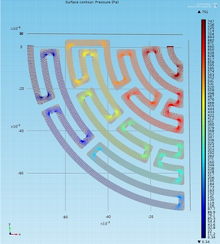
Téléchargement
- kulkarni_abstract.pdf - 0.11MB