- Bridging the Terahertz Gap
- Modeling the Lithium-Ion Battery
- Protection contre la Corrosion
- Modélisation des batteries
- Modélisation et Simulation dans le développement des piles à combustible
- Modélisation thermique des petits satellites
- Analyse électro-vibroacoustique d'un transducteur à armature équilibrée
CFD Simulation of Coolant Flow of 2nd Generation HFIR Irradiation Target Holder
A 2nd-generation irradiation target holder is being developed at the High Flux Isotope Reactor (HFIR) of Oak Ridge National Laboratory (ORNL). This 2nd-generation holder design is focused on improving the loading and unloading of the targets by the HFIR operators since a large number of targets are anticipated to be irradiated in the future. Part of the safety analysis required is to ensure an adequate cooling for the seven targets which requires receiving 5 gpm of coolant flow to each target. In this work, two flow models representing the flow over the targets are built using the COMSOL Multiphysics® software. The first model (Model-1) represents a pie sector of the full configuration of the targets holder flow channel, whereas the second model (Model-2) focuses only on the flow channel over the outer targets. The main objective of both models is to ensure an adequate flow rate distribution over each channel and determine the local distribution of the water flow over the outer channel, in addition to determining the surface temperature of the irradiated targets. CFD simulations using RANS k-ε turbulent model have shown reduced flow into the center target and the inner side of the outer targets channel flow. A multi-physics model that includes the heat flux produced by the targets is to be included to understand the impact of the flow rate variations on the targets surface temperature.
Introduction: Material irradiation at High Flux Isotope Reactor (HFIR) at Oak Ridge National Laboratory (ORNL) requires the material to be placed in close proximity to the nuclear reactor core. In the current process, the material to be irradiated is mixed and compressed in a metallic powder to form a pellet; several pellets are stacked together inside a slender cylindrical housing to form what is referred to here as a target. Seven of these cylindrical targets are combined and held together with one target holder as shown in Figure 1; this assembly fits inside one of the small vertical experiment facility (VXF) of the HFIR. The current target holder design poses multiple challenges regarding manufacturing, assembly and disassembly processes. A new target holder is being developed; the objective of the new design is to address those challenges and simplify the overall work flow. Part of the safety analysis required is to ensure sufficient cooling for the targets. In this work, two flow models represent the flow over the targets are built using the COMSOL Multiphysics® software. The main objective of both models is to ensure adequate flow distribution over each channel and determine the local distribution of the water flow over the outer channel, in addition to determining the surface temperature of the irradiated targets. Model-1 is a one-sixth slice of the entire flow channel inside the 2nd generation holder (Figure 2). The model is constructed with minimal simplifications to the actual design. A one-sixth sector is chosen to preserve the quasi-axisymmetric flow while allowing for higher density meshing. Model-2 is focused on the flow on the outer six targets. Because of symmetry, half of one outer target is sufficient to represent the flow over the outer targets. This model is used to simplify the complex geometry so that the focus remains on the local flow rate distribution and the heat convection process.
USE OF THE COMSOL MULTIPHYSICS® SOFTWARE: Flow models presented here are solved using turbulent CFD modules k-ε and SST to determine the flow rate average and local distribution and pressure drop. The solutions are then coupled with heat transfer module to simulate the cooling process to determine the targets surface temperature. All simulations are computed using cluster facilities at ORNL [1].
Results: Initial flow simulations have shown consistent overall pressure drop across the outer target flow for both simulations which is also consistent with the current design. In the Model-1-CFD case, the target holder configuration (under development) has shown a significant reduction of flow rate to the center target, which has prompted a design change to feed the center target independently. In addition to this, both models Model-1-CFD and Model-2-CFD have indicated slower flow in the inner side of the outer target as seen in Figures 3 and 4. Further investigation is needed to evaluate the impact on the cooling process.
Conclusion: Two flow models are constructed to investigate the flow characteristics of the coolant flow over the seven irradiated targets based on new target holder design. The initial investigation for the flow field showed low flow rate feeding the center target channel and lower flow rate in the inner side of the outer flow channel. As a result, both may require design modifications to guarantee adequate cooling for the targets.
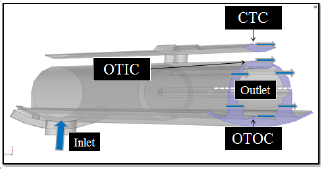
Téléchargement
- elzawawy_poster.pdf - 1.33MB
- elzawawy_abstract.pdf - 0.17MB