- Bridging the Terahertz Gap
- Modeling the Lithium-Ion Battery
- Protection contre la Corrosion
- Modélisation des batteries
- Modélisation et Simulation dans le développement des piles à combustible
- Modélisation thermique des petits satellites
- Analyse électro-vibroacoustique d'un transducteur à armature équilibrée
Design and Simulation of MEMS based Thermally Actuated Positioning Systems
With continuous advancement in nanotechnology, requirement is rising for high precision motion controlled positioning system. Such system plays crucial role in the fabrication of micro and nano-sized objects and assemblies. They can be used for automated mask aligner, as biological sensors, in optical technology as deformable mirrors. Most significant requirements for the actuators in a positioner include accuracy, range of motion, degrees-of-freedom, and bandwidth. While most conventional positioning systems are large in size, a major disadvantage of such macro scale positioners is errors like backlash and hysteresis. However using MEMS technology, such systems can be fabricated in wafers. These micro systems have a number of advantages. Firstly, micro-fabrication permits arrays of MEMS positioning stages to be constructed on a common substrate – Thus allowing highly efficient parallel manipulation. Also, Manipulation capability with multiple degrees-of-freedom (DOF) engaged simultaneously. In this paper, we have addressed the issues related to the design and behavioral simulation of MEMS based thermally actuated positioning system [Figure 1] with motion capabilities in all directions. The central positioning stage is a 250X250 micron square plate made of poly-silicon. The design is done in accordance with the design rules of PolyMUMPs, which is a commercially available multi user three layer poly-silicon MEMS fabrication process. A detailed dimension of the device is shown on Figure 2. The coupled multi physics simulation and study of the electrical, thermal and most importantly, the mechanical behavior of the mirror is done using thermal-electric-structural interaction mode of COMSOL Multiphysics MEMS module. Two types of thermal actuation mechanism are used in the designed device. For in-plane movement poly-silicon made hot arm, cold arm actuator [Figure 3] is used. Here, a hot arm is attached on both sides of a common cold arm. Electric current only passes through one hot arm and the cold arm; this causes that the temperature of the ‘thinner’ hot arm to become much higher than the ‘wider’ cold arm. This difference in temperature causes the hot arm to expand more than the cold arm, which results in the rotation of the actuator. For out-of-plane movement, advantage of difference in the resistivity of two different layers of poly-silicons has been taken [Figure 4]. When current passes through one layer, it warms up more compared to the other and thus bends. In the complete positioning structure, four in-plane and four out-of-plane actuators are attached to the central positioning stage to obtain displacements in all possible directions independently. The simulated structure is capable of producing comparable range of displacements in all possible directions using IC compatible voltages. The range of motion is in the micron order, while the resolution lies in the nanometer scale. The ability of precise control of movement of the positioner in space is likely to lead to potential applications in diverse fields. The use of thermal actuation process limits the bandwidth of the device within the KHz range, which is a typical drawback of such actuation mechanism. This is however offset by the simpler fabrication processes required for these devices.
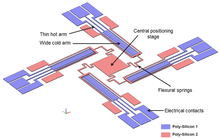
Téléchargement
- mallick_poster.pdf - 0.95MB
- mallick_paper.pdf - 1.39MB
- mallick_abstract.pdf - 0.36MB