- Bridging the Terahertz Gap
- Modeling the Lithium-Ion Battery
- Protection contre la Corrosion
- Modélisation des batteries
- Modélisation et Simulation dans le développement des piles à combustible
- Modélisation thermique des petits satellites
- Analyse électro-vibroacoustique d'un transducteur à armature équilibrée
Design, Simulation, and Fabrication of Thermal Angular Accelerometers
This abstract introduces a sensor design for detecting angular acceleration in a single plane using thermal convection. The working principal of the device is based on probing temperature profile changes along a micro-torus caused by angular acceleration. By properly choosing the locations of the heaters as well as the temperature sensors, the output signal will correlate to in-plane angular acceleration of the micro-structure, while canceling out linear acceleration within the plane. This work demonstrates simulation and experimental results, which provide design guidelines for optimizing the detection of angular acceleration. Measured devices show a sensitivity of 16.1µV/rad/s^2, and a frequency response of DC to 80Hz, while consuming a non-optimized 1.2mW.
The design comprises four or more linear thermal accelerometers that are placed along the circumference of a micro-machined torus to detect the tangential acceleration along the torus. The tangential acceleration relates to the angular acceleration though α = a/R, where α, a, and R are the angular acceleration, tangential acceleration, and major radius of the torus, respectively. Each of the four linear accelerometers consists of a central heating resistor and two symmetrically-arranged, resistive temperature probes that monitor the temperature profile generated by the heater. A clockwise angular acceleration applied to the structure increases the temperature of the four upstream probes while the four downstream probes experience a temperature decrease. Thus, the resulting temperature difference is a measure of the applied (tangential) acceleration. An angular acceleration yields the same output for all four sensors, while linear accelerations can be distinguished by their characteristic response patterns. In addition, a closed torus structure (similar to the semicircular canals of the vestibular system) is intrinsically insensitive to linear accelerations. The geometry of the individual sensors, e.g., the distance between heater and T-probe, was optimized using COMSOL Multiphysics® software.
Figure 1 shows an optical image of a fabricated angular accelerometer design with R=2.85mm. Figure 2 shows the response of a single sensor to angular acceleration; the particular design had an etched channel depth of 350µm and a main radius R = 2500µm. A rate table was used to apply different angular accelerations with a frequency of 2Hz. The measured device sensitivity is 16.1 µV/rad/s2.
COMSOL Multiphysics was used to simulate the device using the Conjugate Heat Transfer physics interface. Initial device simulations were performed on a 3D linear structure: to this end, the torus was unwrapped and turned into a linear pipe, with periodic boundary conditions for fluid flow and heat transport being applied to the ends of the device, as shown in Figure 3. Subsequently, a comprehensive 3D torus model was simulated. Fig. 4 shows the temperature distribution in the center of the pipe around the heating element for the cases of zero applied angular acceleration and α = 1000 deg/s2. From the difference of both temperature profiles, the optimal distance between heater and T-probe can be deduced.
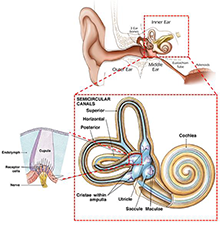
Téléchargement
- alrowais_poster.pdf - 0.8MB
- alrowais_abstract.pdf - 2.58MB