- Bridging the Terahertz Gap
- Modeling the Lithium-Ion Battery
- Protection contre la Corrosion
- Modélisation des batteries
- Modélisation et Simulation dans le développement des piles à combustible
- Modélisation thermique des petits satellites
- Analyse électro-vibroacoustique d'un transducteur à armature équilibrée
Multiscale Resin Impregnation Modeling in a Bidirectional Composite Laminate
Resin Transfer Molding (RTM), is a closed mold reinforced polymer composite molding process where the resin is infused under a pressure gradient. The liquid resin is infused through the dry preform and displaces air to saturate the preform. One of the governing parameters in an RTM process is the inlet pressure; the flow of the resin differs depending on the pressure used. The dual-scale porous media flow comprises of inter-tow flow (flow between the tows in inter-tow region, Figure 1) governed primarily by injection pressure, and intra-tow flow (flow within the tows in intra-tow region, Figure 2) governed by injection pressure as well as capillary action due to surface tension. Voids are formed as the flow progresses, due to the non-uniformity of the inter-tow and intra-tow flow fronts. When the resin flows around the tows before permeating through it, the voids are trapped within the tows. In reverse case, at low pressure and low filling velocities, capillary forces may cause the flow of the resin primarily within the fibre bundles which could lead to void formation in the inter-tow region. This article presents a study of flow-front progression in the inter-tow and intra-tow regions with an aim to understand the optimum parameters for a uniform flow-front, thus reducing the void content through the laminate. The study is a 3D time-dependent multi-scale model of the process of resin impregnation through a layup of bidirectional fibre preform fabric at both inter-tow and intra-tow domains. The multiphase flow of resin through this fabric was modeled as a flow through porous media at the two length scales using the Subsurface Flow module in COMSOL Multiphysics®. The time-dependent study provided the spatial evolution of resin saturation state as a function of process time. Performance of composite laminates greatly depends on optimum fabrication process parameters and can be compromised due to process-induced defects like voids and dry-spots. The study of the resin flow dynamics with respect to the fabric tow interaction, along with other parameters such as vent pressure, inlet pressure, temperature and gate positioning can greatly result in a uniform flow front development. The current study will provide a better understanding of the flow behavior within the tows and outside, thus resulting in an optimized process window that would aid in fabricating a composite laminate with reduced void content.
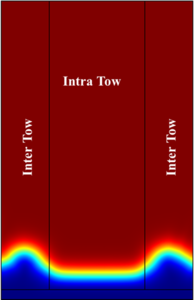
Téléchargement
- mishra_presentation.pdf - 1.01MB
- mishra_abstract.pdf - 0.15MB