- Bridging the Terahertz Gap
- Modeling the Lithium-Ion Battery
- Protection contre la Corrosion
- Modélisation des batteries
- Modélisation et Simulation dans le développement des piles à combustible
- Modélisation thermique des petits satellites
- Analyse électro-vibroacoustique d'un transducteur à armature équilibrée
Simulation of a Buckled Cantilever Plate with Thermal Bimorph Actuators
INTRODUCTION: Micro Electro Mechanical Systems (MEMS) are fabricated with an in-plane fabrication technology. Out-of-plane structures can be designed to be assembled to provide thermal and electrical isolation from the substrate [1 -3]. These isolations can potentially improve the performance of a range of MEMS devices by decreasing any unwanted coupling effects or parasitic losses from the devices to a lossy substrate. One of the interesting out-of-plane mechanism is the Buckled Cantilever Plate (BCP) [1,3,4] and the other one is the Tsang Suspension [5,6]. We have designed and simulated BCP out-of-plane structures with thermal dimorph actuators to be able to control the angular position of the assembled plate Fig. 1.
RESULTS: For the COMSOL Multiphysics® simulation we first created a 3D model of the structure in the COMSOL environment. Each domain was assigned its corresponding material, using Polyamide as the structural layer. We use setup the boundary condition that represent the physical assembly using the Solid Mechanics interface. Anchors were fixed and the free end edge was given a prescribed displacement in the Y-axis. A second study is performed to simulate the heat transfer physics using the Thermal Expansion interface. Boundary conditions applicable to the study such as: the structure temperature, environment temperature, the heat fluxes present in the system and heat flux dissipation were set accordingly. In Fig. 2 we can see the results of the simulation of an assembled BCP with bimorph actuators active.
CONCLUSION: COMSOL Multiphysics simulations gave good agreement with our experimental results. Our next steps are to simulate more designs and use this validated model as a design tool to help in the optimization of the design parameters.
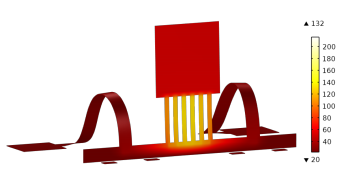
Téléchargement
- arevalo carreno_presentation.pdf - 21.53MB
- arevalo carreno_poster.pdf - 1.62MB
- arevalo carreno_paper.pdf - 2.79MB
- arevalo carreno_abstract.pdf - 0.3MB