Evènements
Méthodologie de modélisation
Electromagnétisme
Structure & acoustique
Fluide & thermique
Chimie
Interfaces
Général
Affichage:
Fuseau horaire:
Mon fuseau horaire (CEST)
Horaire organisateur
08:00 AM - 08:00 PM
Evènements démarrant entre: 08:00 – 20:00
Recherche
Evènements à venir
Chargement des Évènements

juil. 17
| 15:00 BST
Biomedical Modeling with COMSOL Multiphysics
COMSOL
Webinaire
En ligne
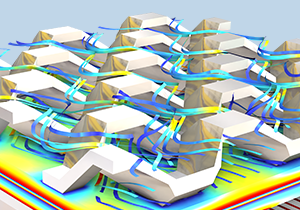
juil. 22
| 14:00 CEST
Solving Large Models in COMSOL Multiphysics®
COMSOL
Webinaire
En ligne
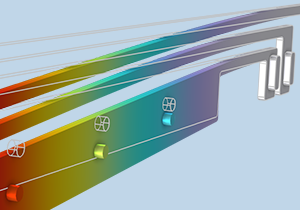
juil. 22–25
| 17:00 EDT
Introduction to COMSOL Multiphysics®
COMSOL
Formation
En ligne

juil. 22
| 20:00 EDT
Modeling Next-Generation Battery Technologies with COMSOL Multiphysics®
Battery Technology
Webinaire
En ligne
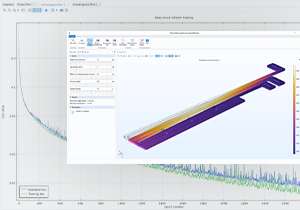
juil. 24
| 11:00 CEST
Comment créer des modèles de substitution avec COMSOL Multiphysics®
COMSOL
Webinaire
En ligne

juil. 24
| 20:00 EDT
Digital Twin Modeling of Human Thorax for HFCC Therapy Using COMSOL Multiphysics®
IEEE
Webinaire
En ligne
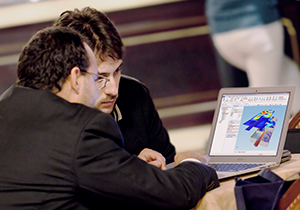
juil. 28–29
| 09:00 CEST
COMSOL Multiphysics® Intensive Training (2 Days)
COMSOL
Formation
Zoetermeer

juil. 29
| 20:00 EDT
Multiphysics Modeling of Power Electronics
COMSOL
Webinaire
En ligne
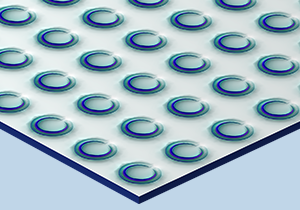
juil. 31
| 15:00 BST
Modeling Acoustic Metamaterials in COMSOL Multiphysics
COMSOL
Webinaire
En ligne

août 5–7
| 10:30 BST
(Online) Introduction to COMSOL Multiphysics® (3 Days)
COMSOL
Formation
En ligne
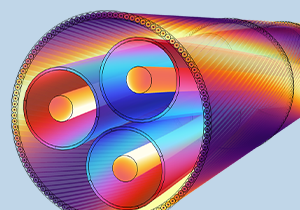
août 5
| 14:00 CEST
Simulating Electrical Power Systems for the Grid
COMSOL
Webinaire
En ligne
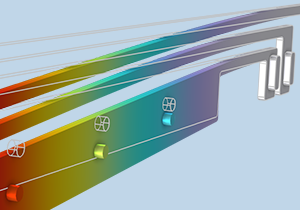
août 5
| 17:30 EDT
The Basics of COMSOL Multiphysics® in 18 Minutes
COMSOL
Webinaire
En ligne

août 7
| 20:00 EDT
Moisture Transport Modeling in COMSOL Multiphysics®
COMSOL
Webinaire
En ligne
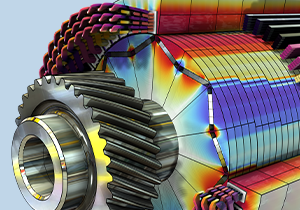
août 14
| 15:00 BST
Modeling and Simulation for Electric Motor Design
COMSOL
Webinaire
En ligne
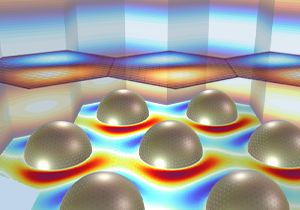
août 14
| 20:00 EDT
Modeling Periodic Structures in RF and Optics
Physics Today
Webinaire
En ligne

août 18–25
| 11:00 IST
Training Course: Modeling Plasma in COMSOL Multiphysics®
COMSOL
Formation
En ligne
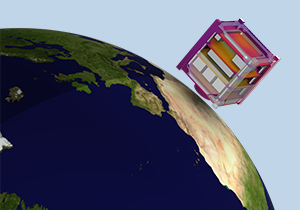
août 19
| 14:00 CEST
Analyzing Spacecraft Thermal Performance
COMSOL
Webinaire
En ligne

août 19
| 20:00 EDT
Modeling Room Acoustics in COMSOL Multiphysics®
COMSOL
Webinaire
En ligne
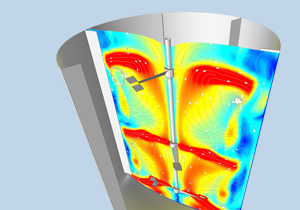
août 20
| 10:00 CEST
Atelier d'Introduction à la Suite Logicielle COMSOL®
COMSOL
Workshop
En ligne

août 26–29
| 17:00 EDT
AC/DC Modeling in COMSOL Multiphysics®
COMSOL
Formation
En ligne

août 28
| 15:00 BST
Prediction of Electromagnetic Signatures of Naval Vessels with COMSOL Multiphysics
COMSOL
Webinaire
En ligne

sept. 2–4
| 10:30 BST
(Online) Introduction to COMSOL Multiphysics® (3 Days)
COMSOL
Formation
En ligne

sept. 2
| 14:00 CEST
Design Optimization for Engineering Problems
COMSOL
Webinaire
En ligne

sept. 3
| 15:00 BST
Optimization of Thermal Management Systems
COMSOL
Webinaire
En ligne
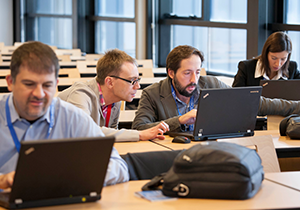
sept. 8–9
| 09:00 CEST
On-site: Heat Transfer Intensive Training Course (2 Days) - Zurich
COMSOL
Formation
Zurich
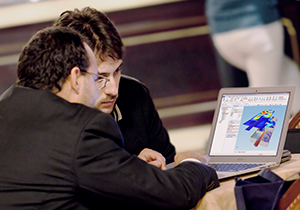
sept. 9
| 08:00 EEST
COMSOL Multiphysics Open Training
COMSOL
Training
Espoo
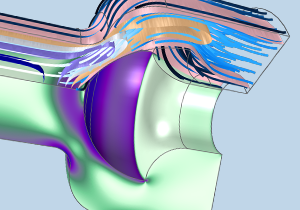
sept. 9–12
| 17:00 EDT
CFD Modeling in COMSOL Multiphysics®
COMSOL
Formation
En ligne

sept. 10
| 10:00 CEST
Atelier d'Introduction à la Suite Logicielle COMSOL®
COMSOL
Workshop
En ligne
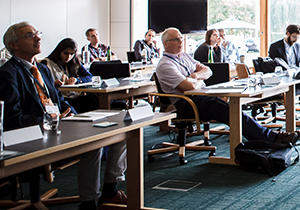
sept. 16–18
| 09:00 CEST
Formation Intensive en Ligne à COMSOL Multiphysics® 2 jours
COMSOL
Formation
En ligne
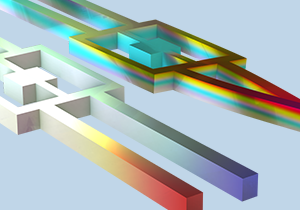
sept. 16–19
| 17:00 EDT
Structural Mechanics Modeling in COMSOL Multiphysics®
COMSOL
Formation
En ligne
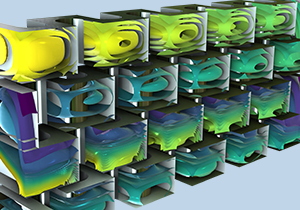
sept. 23
| 14:00 CEST
Process Engineering: Fluid Flow & Chemical Reactions
COMSOL
Webinaire
En ligne
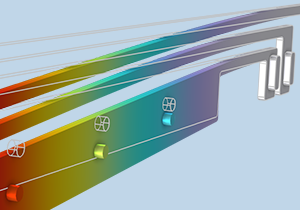
sept. 23–26
| 17:00 EDT
Introduction to COMSOL Multiphysics®
COMSOL
Formation
En ligne

sept. 23
| 20:00 EDT
Modeling and Simulation of MEMS Devices
COMSOL
Webinaire
En ligne
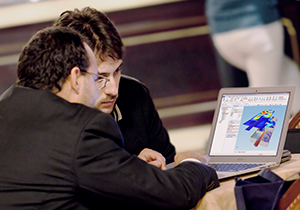
sept. 24
| 08:30 EEST
Open Training: Introduction to modern simulation workflow
COMSOL
Training
Tampere
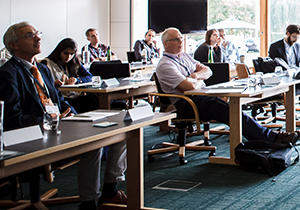
sept. 29–30
| 09:00 CEST
COMSOL Multiphysics® Intensive Training (2 Days)
COMSOL
Formation
Zoetermeer

oct. 1
| 10:00 CEST
Atelier d'Introduction à la Suite Logicielle COMSOL®
COMSOL
Workshop
En ligne
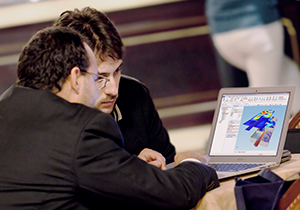
oct. 2
| 09:00 CEST
COMSOL Multiphysics® : Formation en ligne au module RF
COMSOL
Formation
En ligne
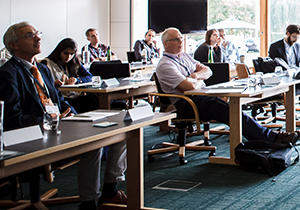
oct. 7–9
| 09:00 CEST
Formation Intensive en Ligne à COMSOL Multiphysics® (2 jours)
COMSOL
Formation
En ligne
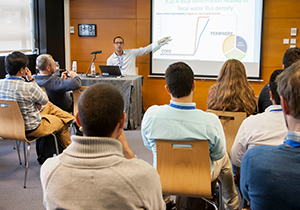
oct. 7–8
| 09:00 CEST
Formation Intensive à COMSOL Multiphysics® EN PRESENTIEL (2 jours)
COMSOL
Formation
GRENOBLE
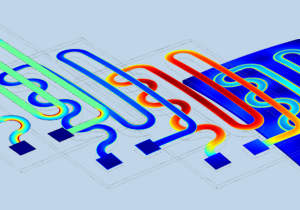
oct. 14–17
| 17:00 EDT
Heat Transfer Modeling in COMSOL Multiphysics®
COMSOL
Formation
En ligne

oct. 21–24
| 17:00 EDT
RF Modeling in COMSOL Multiphysics®
COMSOL
Formation
En ligne
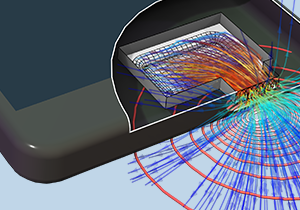
oct. 28–31
| 16:00 EDT
Acoustics Modeling in COMSOL Multiphysics®
COMSOL
Formation
En ligne
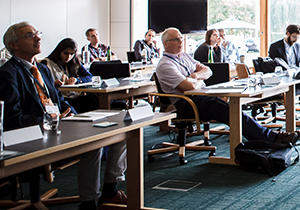
nov. 4–6
| 09:00 CEST
Formation Intensive en Ligne à COMSOL Multiphysics® (2 jours)
COMSOL
Formation
En ligne
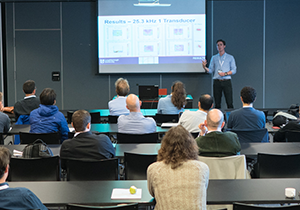
nov. 4–5
| 15:00 EDT
Introduction to COMSOL Multiphysics®
COMSOL
Formation
Burlington
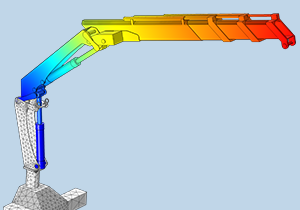
nov. 5
| 10:00 CEST
Atelier d'Introduction à la Suite Logicielle COMSOL®
COMSOL
Workshop
En ligne

nov. 11–14
| 17:00 EDT
Electrochemistry & Electrodeposition Modeling in COMSOL Multiphysics®
COMSOL
Formation
En ligne
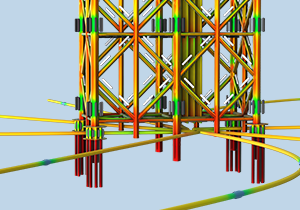
nov. 18–20
| 17:00 EDT
Corrosion Modeling in COMSOL Multiphysics®
COMSOL
Formation
En ligne
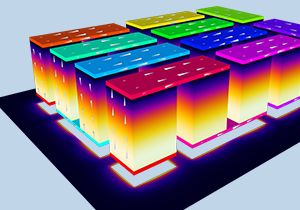
déc. 3
| 10:00 CEST
Atelier d'Introduction à la Suite Logicielle COMSOL®
COMSOL
Workshop
En ligne
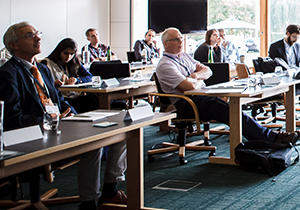
déc. 9–11
| 09:00 CEST
Formation Intensive en Ligne à COMSOL Multiphysics® (2 jours)
COMSOL
Formation
En ligne
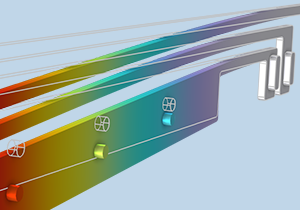
déc. 9–12
| 17:00 EDT
Introduction to COMSOL Multiphysics®
COMSOL
Formation
En ligne
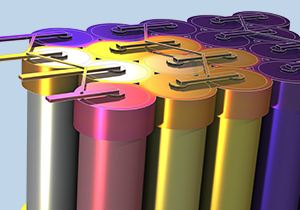
déc. 16–19
| 17:00 EDT
Battery Modeling in COMSOL Multiphysics®
COMSOL
Formation
En ligne
Affichage de 8 sur 51 évènements
Affichage de 51 sur 51 évènements
Webinaires à la demande
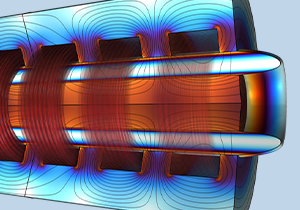
Understanding Liquid Metal Transport in Magnetic Fields — Simulating Magnetohydrodynamic Duct Flow
Webinaire
Jul 11

Créer des applications de simulation et des jumeaux numériques avec COMSOL Multiphysics®
Webinaire
Jul 10

Memristor Modeling with COMSOL Multiphysics®
Webinaire
Jul 02
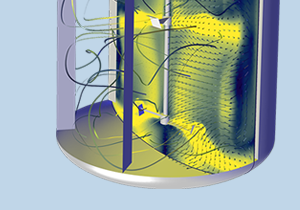
Modeling Fluid Mixers and Stirred Tank Reactors in COMSOL Multiphysics®
Webinaire
Jun 26

Underwater Acoustics
Webinaire
Jun 12

Optimization in Structural Mechanics
Webinaire
Jun 12
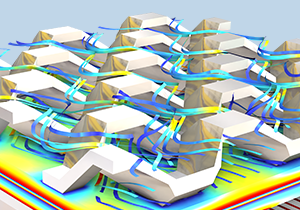
Hydrogen Technology Innovation with Simulation
Webinaire
Jun 12
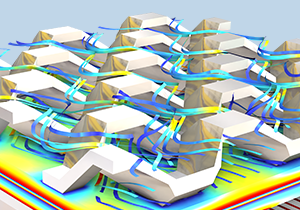
Modeling Hydrogen Fuel Cells and Electrolyzers
Webinaire
Jun 12
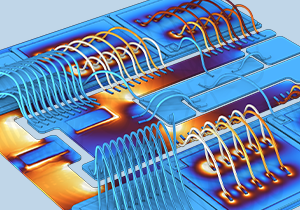
Améliorer la gestion thermique des dispositifs électroniques avec COMSOL Multiphysics®
Webinaire
Jun 12
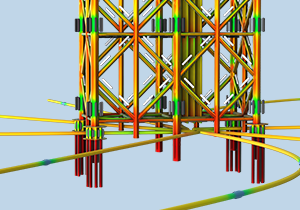
Modeling Chemical Reactions and Reacting Flows Using COMSOL Multiphysics®
Webinaire
Jun 05

Introduction to Multibody Dynamics Modeling with COMSOL Multiphysics
Webinaire
May 28

Automotive Acoustics Analysis Using COMSOL Multiphysics®
Webinaire
May 27

Comment faire de l’optimisation et de l’estimation de paramètres avec COMSOL Multiphysics®
Webinaire
May 22

Acoustics in Electronics Series, Part 4: Piezoelectric Devices
Webinaire
May 20
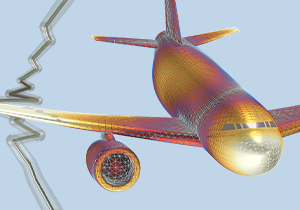
Modélisation multiphysique pour l’aéronautique et le spatial avec COMSOL Multiphysics®
Webinaire
May 13

Improving Thermal Management of Batteries with COMSOL Multiphysics®
Webinaire
May 09

Acoustics in Electronics Series, Part 3: Hearing Aids
Webinaire
May 06

Comment utiliser le solveur temporel de COMSOL Multiphysics®
Webinaire
Apr 24
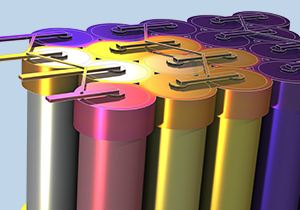
Modéliser les Batteries avec COMSOL Multiphysics®
Webinaire
Apr 17

Acoustics in Electronics Webinar Series, Part 2: MEMS Speakers and Microphones
Webinaire
Apr 16

The Basics of COMSOL Multiphysics® in 18 Minutes
Webinaire
Apr 15

Optimization in RF and Wave Optics
Webinaire
Apr 09

Wave & Ray Optics Modeling with COMSOL®
Webinaire
Apr 09

Meshing Your Models in COMSOL Multiphysics®
Webinaire
Apr 08

Multiphysics Simulation in Semiconductor Packaging
Webinaire
Apr 03

Acoustics in Electronics Webinar Series, Part 1: Loudspeakers
Webinaire
Mar 25
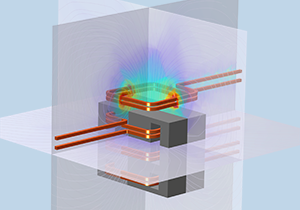
Simulating Electrical Power Systems for the Grid
Webinaire
Mar 20
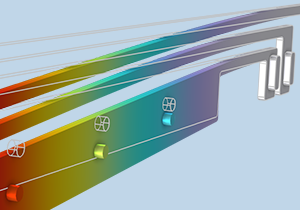
Comment Utiliser Efficacement les Études Stationnaires de COMSOL Multiphysics®
Webinaire
Mar 20
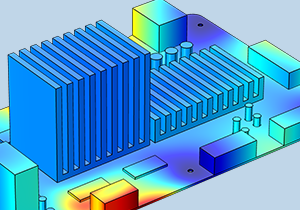
Multiphysics Modeling of Electronic Components
Webinaire
Mar 20

Using Geometry Modeling Tools in COMSOL Multiphysics®
Webinaire
Mar 18

Improving Thermal Management of Batteries with COMSOL Multiphysics®
Webinaire
Mar 18

Modéliser les Composants Électroniques avec COMSOL Multiphysics®
Webinaire
Mar 13

Modeling Chemical Reactions and Reacting Flows Using COMSOL Multiphysics®
Webinaire
Mar 06

Integrating Frequency-Dependent Data into Time-Domain Acoustics Analysis
Webinaire
Feb 27
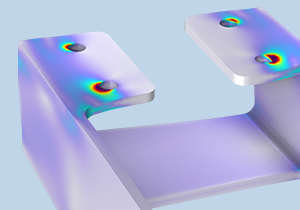
Introduction to Uncertainty Quantification
Webinaire
Feb 26

Efficient Battery Modeling with Surrogate Models
Webinaire
Feb 18

Comment construire un maillage dans COMSOL Multiphysics®
Webinaire
Feb 18
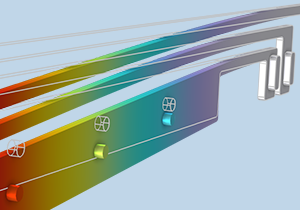
The Basics of COMSOL Multiphysics® in 18 Minutes
Webinaire
Feb 13
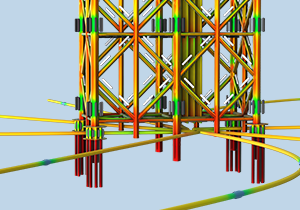
Modéliser la Corrosion et les Systèmes de Protection contre la Corrosion avec COMSOL Multiphysics®
Webinaire
Feb 13
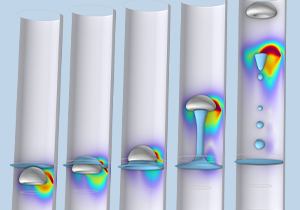
Designing a Magnetorheological-Fluid-Based Clutch Using COMSOL Multiphysics®
Webinaire
Feb 13

Modeling Biochemical Sensors and Testing Devices with COMSOL®
Webinaire
Jan 29
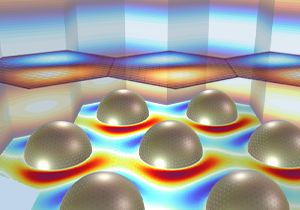
Modeling Optical Nanostructures with COMSOL Multiphysics®
Webinaire
Jan 23
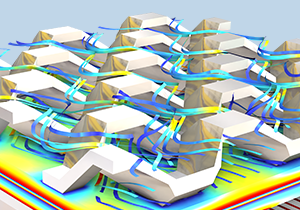
Améliorer les Performances des Piles à Combustible et des Électrolyseurs avec COMSOL Multiphysics®
Webinaire
Jan 23

Electric Discharge Modeling
Webinaire
Jan 21

Automotive Acoustics Analysis Using COMSOL Multiphysics®
Webinaire
Jan 16
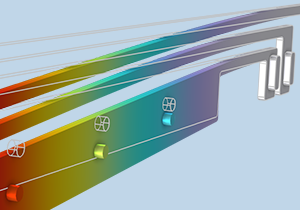
The Basics of COMSOL Multiphysics® in 18 Minutes
Webinaire
Jan 14

Comment Construire efficacement sa Géométrie avec le Module Design
Webinaire
Jan 14

Multiphysics Fracture Mechanics with COMSOL Multiphysics® in 18 minutes
Webinaire
Dec 12

Models for Transport and Chemistry in CVD Reactors
Webinaire
Dec 05

Modéliser les Procédés de Fabrication avec COMSOL Multiphysics®
Webinaire
Dec 05

Modeling Nanophotonic Applications with COMSOL Multiphysics®
Webinaire
Nov 28

Design Optimisation for Engineering Problems
Webinaire
Nov 27
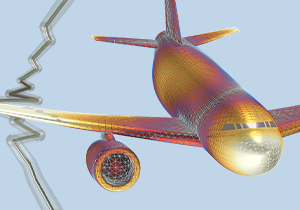
Modélisation Multiphysique pour l’Aéronautique et le Spatial avec COMSOL Multiphysics®
Webinaire
Nov 21
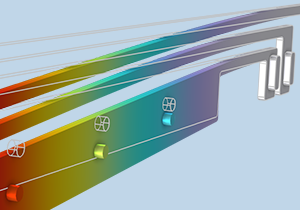
Modeling Shape Memory Alloys and Triboelectric Nanogenerators with COMSOL Multiphysics®
Webinaire
Nov 21

Introducing COMSOL Multiphysics® Version 6.3
Webinaire
Nov 20

Improving Thermal Management of Batteries with COMSOL Multiphysics®
Webinaire
Nov 19
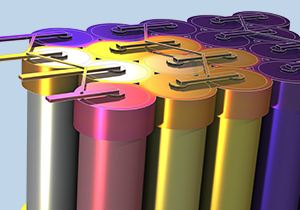
Battery Modeling with COMSOL Multiphysics®
Webinaire
Nov 14

Modéliser les Milieux Poreux avec COMSOL Multiphysics®
Webinaire
Nov 14
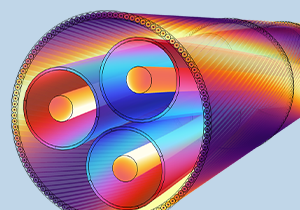
Modeling Cables & Power Electronics
Webinaire
Nov 13

Improving the Manufacturing of Semiconductors with Multiphysics Simulation
Webinaire
Nov 07
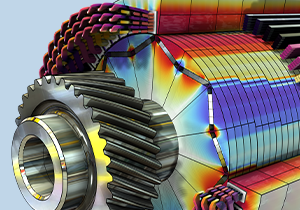
Advancements in Simulation for EV Motors
Webinaire
Nov 06
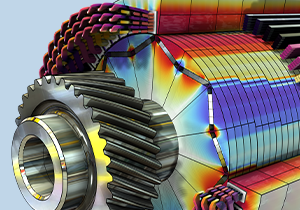
Multiphysics Modeling of Electrical Motors
Webinaire
Oct 31

Modelling the Thermomechanical Behaviour of Glass Materials
Webinaire
Oct 23

Fatigue and Durability Analysis using COMSOL Multiphysics®
Webinaire
Oct 23
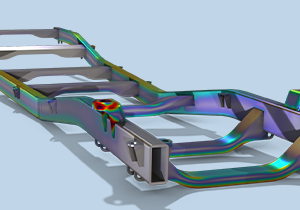
Multiphysics Modeling of Manufacturing Processes Using COMSOL®
Webinaire
Oct 17

Déployer les Bénéfices de la Simulation à l’aide d’Applications Autonomes
Webinaire
Oct 17

Simulating Electromagnetic Metamaterials in COMSOL Multiphysics®
Webinaire
Oct 15
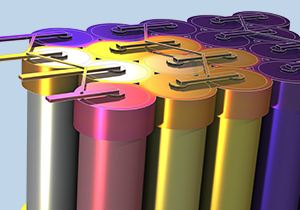
Modeling Thermal Runaway and Abuse in Batteries
Webinaire
Oct 15

Simulating Electronics Packaging and Testing
Webinaire
Sep 26

Electromagnetics Simulation of Printed Circuit Boards in COMSOL Multiphysics®
Webinaire
Sep 26

Simulating Droplet Flow in Wearable Sweat Collection Patches
Webinaire
Sep 25
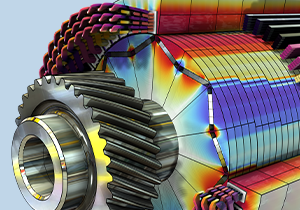
Designing Electric Motors and Drivetrains with Multiphysics Simulation
Webinaire
Sep 20
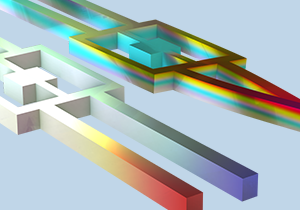
Modeling and Simulation of MEMS Devices
Webinaire
Sep 19
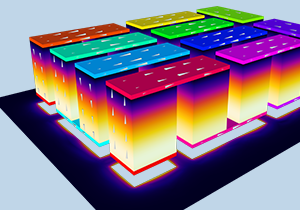
Equation-Based Modeling with COMSOL Multiphysics®
Webinaire
Sep 18
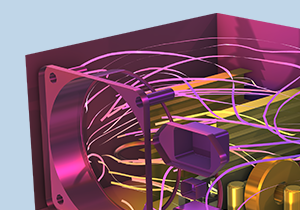
Thermal Management in Electronic Devices with COMSOL Multiphysics®
Webinaire
Sep 18

Battery Modeling with COMSOL Multiphysics®
Webinaire
Sep 17

Simulation Multiphysique, Modèle de Substitution et Jumeaux Numériques
Webinaire
Sep 17
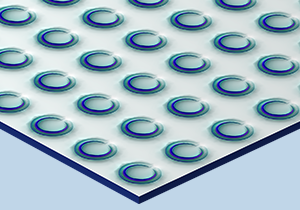
Simulating Plasmonics and Metamaterials
Webinaire
Sep 12
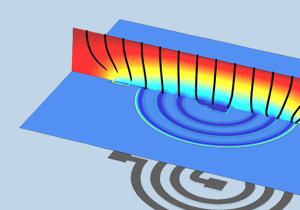
Modeling and Simulation of Electrodeposition Cells
Webinaire
Aug 29
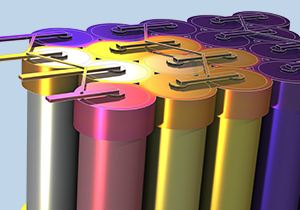
Designing Batteries with Modeling and Simulation
Webinaire
Aug 28

Multiphysics Modeling and Simulation for 5G Devices
Webinaire
Aug 27
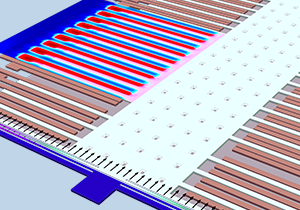
Modeling Low-Frequency Accelerometers Using COMSOL Multiphysics®
Webinaire
Aug 22
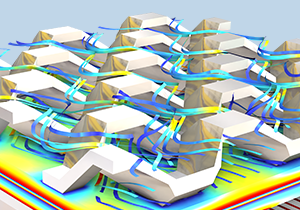
Modeling Hydrogen Production, Storage and Utilization
Webinaire
Aug 21
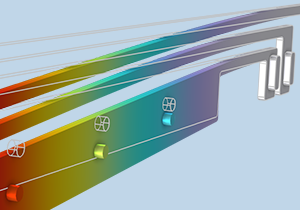
The Basics of COMSOL Multiphysics® in 18 Minutes
Webinaire
Aug 20
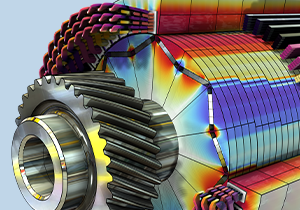
Modeling Electric Motors and Drivetrains
Webinaire
Aug 20

Phased Array Antenna Modeling with COMSOL Multiphysics®
Webinaire
Aug 13
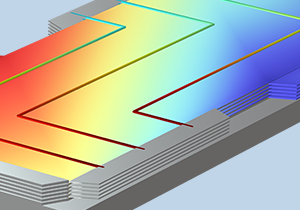
Virtual Hydrogen Lab: Computational Predictions of Hydrogen Uptake, Diffusion, and Embrittlement
Webinaire
Aug 08

Modeling Fluid-Structure Interaction with COMSOL Multiphysics®
Webinaire
Jul 30

Multiphysics Simulation to Improve Design of Renewable Energy Production
Webinaire
Jul 25
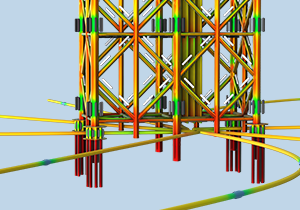
Multiphysics Simulation for Oil & Gas Processing
Webinaire
Jul 19

Modeling Hydrogels and Swollen Elastomers in COMSOL Multiphysics®
Webinaire
Jul 18
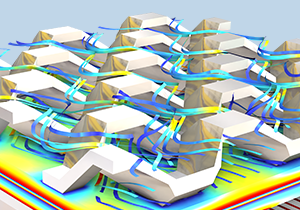
Modeling Hydrogen Fuel Cells and Electrolyzers
Webinaire
Jul 17

Modeling Magnetostrictive Material-Based Energy Harvesting Devices
Webinaire
Jul 17
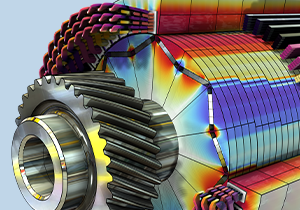
Improving Electric Drivetrain Efficiency with Multiphysics Simulation
Webinaire
Dec 15
Affichage de 6 sur 94 évènements
Affichage de 94 sur 94 évènements
- Informations Produit
- Produits
- Grille des Spécifications
- Types de Licence
- Configuration Requise
- Historique des Versions
- Société
- A propos de COMSOL
- Carrières
- Presse
- Contact
- |
- Politique de confidentialité
- |
- Trademarks
- |
- Cookie Settings
- © 2025 by COMSOL. Tous Droits réservés