Optimizing a Flywheel Profile
Application ID: 4356
This example solves the problem of finding the optimal thickness profile of a flywheel, so that the moment of inertia is maximized without increasing the mass or the maximum stress in the flywheel.
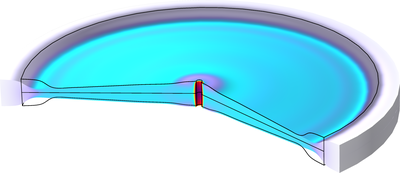
This model example illustrates applications of this type that would nominally be built using the following products:
however, additional products may be required to completely define and model it. Furthermore, this example may also be defined and modeled using components from the following product combinations:
- COMSOL Multiphysics® et
- Module Optimization et
- soit le Module Acoustics, Module MEMS, Module Multibody Dynamics, ou Module Structural Mechanics
The combination of COMSOL® products required to model your application depends on several factors and may include boundary conditions, material properties, physics interfaces, and part libraries. Particular functionality may be common to several products. To determine the right combination of products for your modeling needs, review the Grille des Spécifications and make use of a free evaluation license. The COMSOL Sales and Support teams are available for answering any questions you may have regarding this.